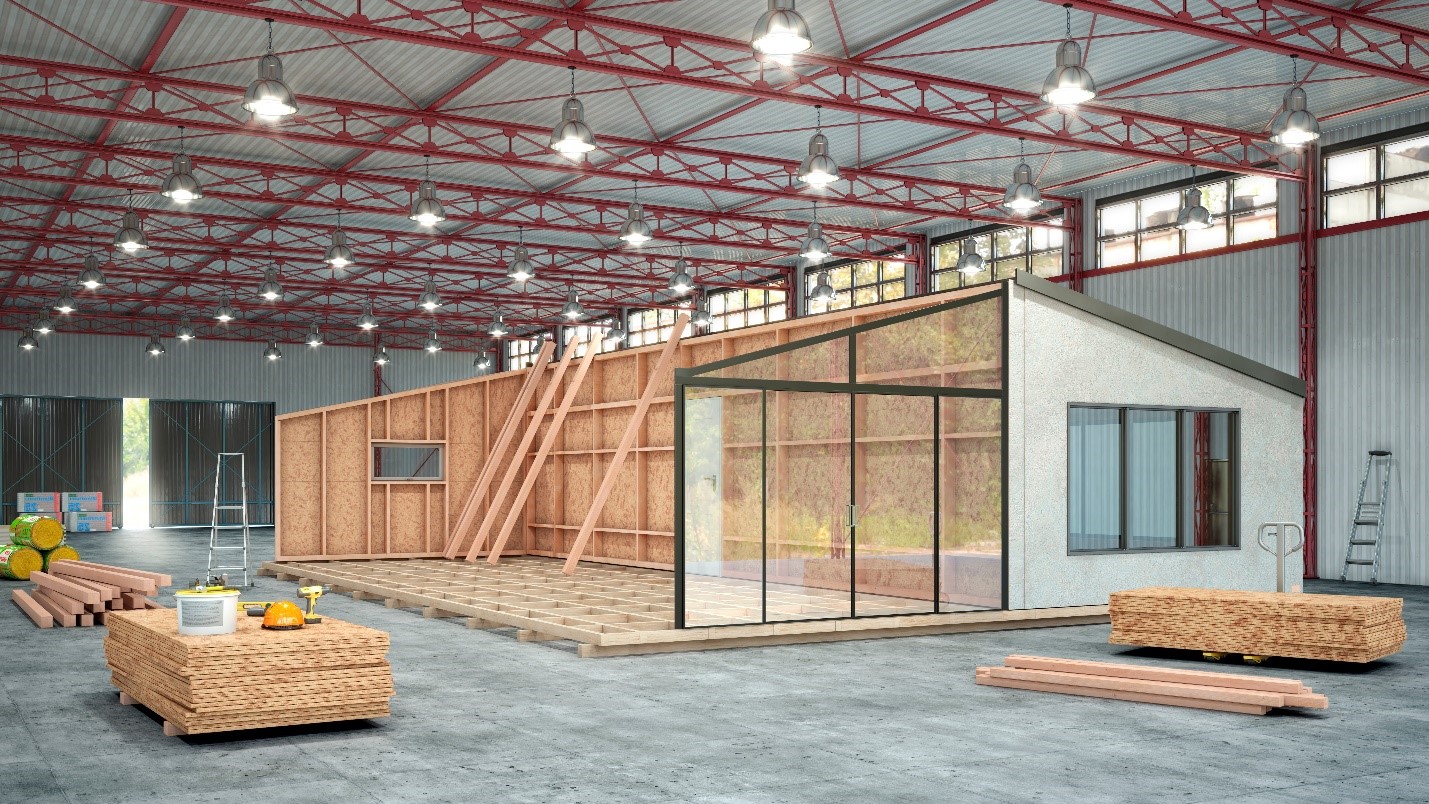
Manufactured Homes: A Guide to Foundation and Support Systems
Are you looking to build, sell, or refinance a manufactured home? Or are you perhaps interested in purchasing a manufactured home using a mortgage lender?
If you’ve answered yes to either, then you may already know that getting a loan and obtaining insurance for manufactured homes requires some extra steps, compared to traditional homes.
Those steps generally entail a foundation certification or design performed by a licensed Professional Engineer (“PE”) in accordance with the Manufactured Home Construction and Safety Standards (“HUD Code”).
Manufactured homes are regulated at the federal level, and so mortgages written by a lender must be insured by the Federal Housing Administration (“FHA”), a division of HUD. As a condition of providing insurance, the FHA requires that the foundations for new homes be designed by a PE. And, similarly to existing homes, a PE is required to sign off on that a new manufactured home’s foundation meets FHA requirements.
A foundation certificate demonstrates that a manufactured home’s foundation is present, permanent, and functional.
This brief guide is not meant to determine whether a particular foundation system qualifies or meets the criteria for an FHA Title II mortgage. In fact, that’s strictly the responsibility of FHA and its representatives.
This guide is, however, meant to provide helpful information to design professionals, insurance companies, and consumers who are engaged in foundation construction and inspections for manufactured homes.
If you need assistance or feel uncomfortable with the process, don’t hesitate to contact W.D. Hill Engineering. We are more than happy to assist you with obtaining a foundation certification or design for a manufactured home’s foundation.
What is a manufactured home?
Manufactured homes (formerly known as “mobile homes”) are prefabricated in controlled manufacturing environments and are then transported in one or more sections on a permanent steel chassis.
In the US, a manufactured home must be built to HUD Code and must display a red certification label on the exterior of each of its transportable sections.
Manufactured homes and mobile homes are both regulated by HUD. These terms are distinguished from each other only by the year of construction. According to HUD, a factory-built home prior to June 15, 1976, is termed a mobile home, whereas one built after June 15, 1976, is a manufactured home.
Unless inspected and approved by a willing licensed structural engineer, if your mobile home was built before June 15, 1976, it is considered non-conformant with current HUD standards and cannot be accepted as compliant with the HUD code. The FHA does not insure mortgages on manufactured homes built prior to June 15, 1976.
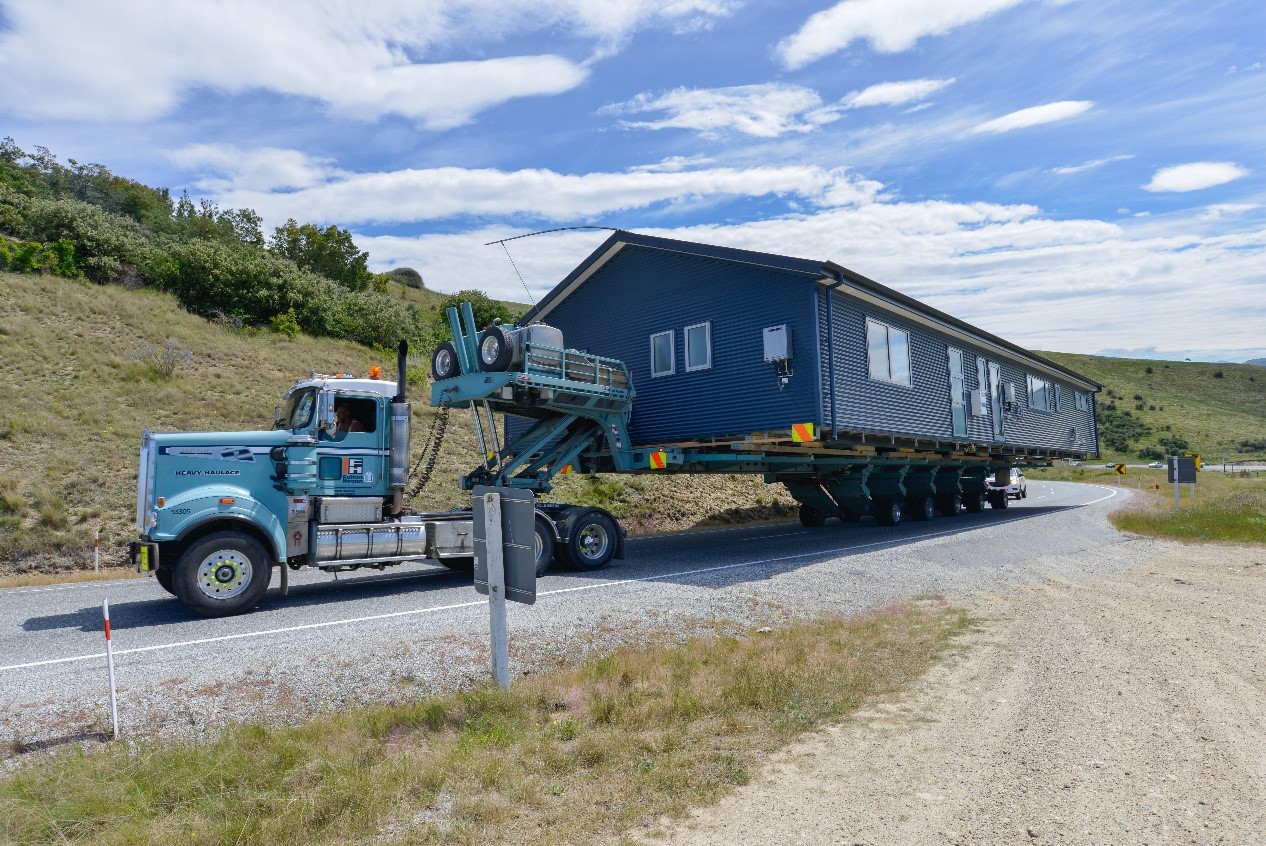
What is a permanent foundation?
According to HUD, a permanent foundation system is defined as follows:
“Permanent foundations must be constructed of durable materials – i.e., concrete, mortared masonry, or treated wood – and be site-built. It shall have attachment points to anchor and stabilize the manufactured home to transfer all loads, herein defined, to the underlying soil or rock. The permanent foundations shall be structurally developed in accordance with this document or be structurally designed by a licensed professional engineer for the following:
1. Vertical stability:
- Rated anchorage capacity to prevent uplift and overturning due to wind or seismic forces, whichever controls. Screw-in soil anchors are not considered a permanent anchorage.
- Footing size to prevent overloading the soil-bearing capacity and avoid soil settlement. Footing shall be reinforced concrete to be considered permanent.
- Base of footing below maximum frost-penetration depth.
- Encloses a basement of crawl space with a continuous wall (whether bearing or non-bearing) that separates the basement of crawl space from the backfill and keeps out vermin or water.
2. Lateral stability. Rated anchorage capacity to prevent sliding due to wind or seismic forces, whichever controls, in the transverse and longitudinal directions.”
As previously mentioned, manufactured homes are built in accordance with the HUD Code. This produces uniformity of construction across state lines. However, while the homes themselves may enjoy consistency of design, foundation plans are subject to review by the authority having jurisdiction (“AHJ”). Foundations must, therefore, be tailored to local site conditions.
Permanent foundations must be designed considering the following site conditions:
- The characteristics of major soil types. Some soils have essentially no ability to support weight. Some react significantly to changes in moisture content, while others are more indifferent. While a detailed geotechnical analysis may not be required, it is prudent to pay careful attention to how your selected foundation system interacts with your local soil types.
- Areas subject to frost heave. Frost is a critical element to consider with any foundation design, and it varies throughout the country. Simply put, frost depth (or line) is the depth in the ground to which water in the soil is known to freeze. When water in soil freezes, it expands and can cause the structure above to shift or heave.
- Foundations must also possess the ability to hold down in hurricane and tropical storm force winds in regions, such as the Southeast, where such storms are commonplace.
- Far northern and mountainous regions can impose heavy snow loads on a roof. These loads are transferred through the structure down to the foundation. In some cases, homes with minimum snow loads (e.g., 20 psf) do not require any perimeter wall support.
Always be sure to discuss site conditions with your building department or engineer when designing and selecting a foundation system for your manufactured home.
Real Property Classification
Real estate professionals refer to “real property” as a parcel of land and everything that is permanently attached to it. The owner of the real property has all rights to possess, sell, lease, and enjoy the land.
Manufactured homes fall into a gray area regarding real property classification. Consequently, classification varies by state and local jurisdictions.
In general, though, a manufactured home is considered “personal property” if it is installed on a temporary foundation. That means it is treated similarly to a vehicle (i.e., it’s mobile).
Manufactured homes classified as personal property must obtain chattel mortgages and are mostly located in land-lease communities.
To receive a conventional mortgage on a manufactured home, in most cases, you must have an HUD-approved permanent foundation affixed. In addition, manufacturers often establish a special set of conditions for foundation systems intended for use with homes financed as real property with a mortgage or deed of trust.
In all cases, real or personal property status is determined by state or local laws. These laws may or may not reference foundation type.
Similarly, eligibility for conventional, long-term financing is determined by underwriting standards that may or may not reference the foundation type or real versus personal property status.
Therefore, you should always confer with local area lenders and real estate professionals on acceptable foundation systems and how they may impact financing options for your home.
Foundation Types
We laid the groundwork by defining manufactured homes, what the HUD considers to be a permanent foundation, and the implications of owning “real property.” Let’s now move on to discuss various popular foundation types and their key attributes.
The table shown below (courtesy of “Guide to Foundation and Support Systems for Manufactured Homes,” prepared by Manufactured Housing Research Alliance) provides a terrific summary of various foundation systems and their compatibility with local site conditions.
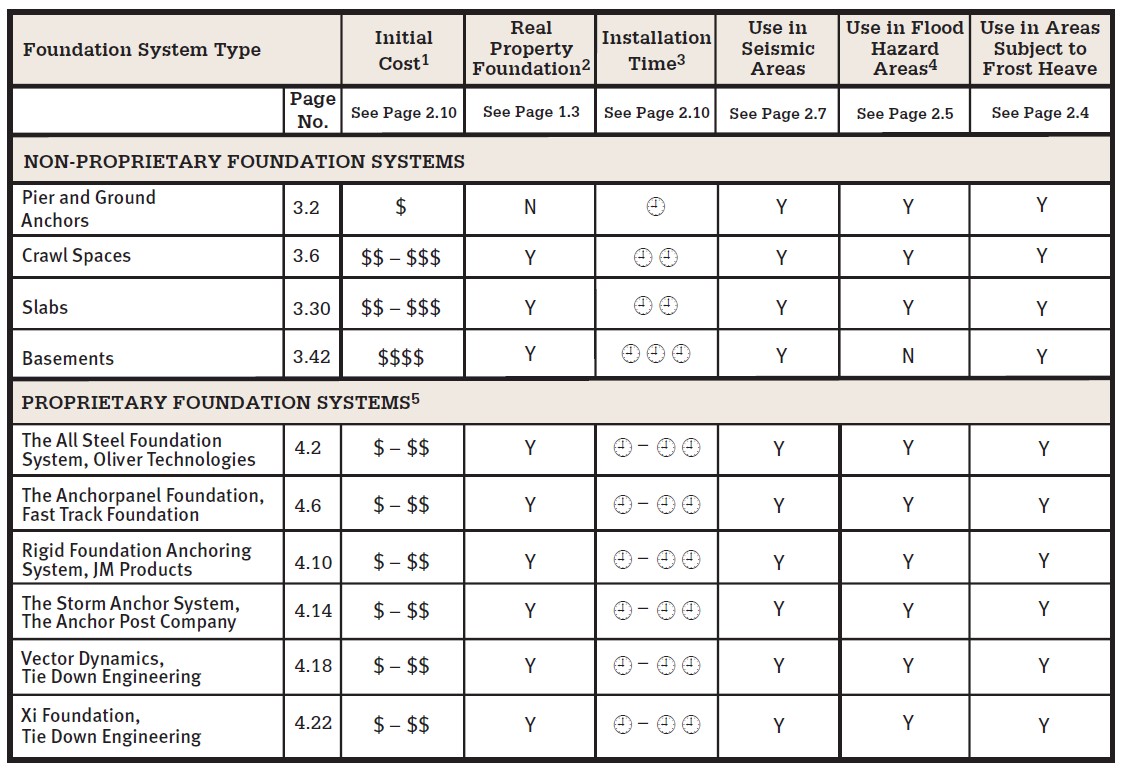
As you can see, the table is split between non-proprietary and proprietary systems. Non-proprietary systems are built with readily available materials and include pier ground anchor systems, crawl space systems, slabs-on-grounds, and basements.
On the other hand, proprietary systems are products manufactured by companies who own a patent or some other protectable interest. Whether you choose to select a non-proprietary or proprietary system, your foundation system should be safe, durable, and long-lasting.
Unlike conventional wood-framed dwellings, manufactured homes are extremely lightweight. That means manufactured homes can be easily lifted, overturned, or slid horizontally. That is why vertical and horizontal anchorage is critical for any manufactured home’s foundation system.
HUD code outlines minimum anchorage requirements for all foundation types.
The HUD Code also goes on to define the following foundation types and structural characteristics as follows (see Figures 1, 2 & 3 for definitions):
- Anchorage: Mechanical connection between superstructure and foundation, by means of welds, bolts, and various light gauge material plates. Note: Anchorage does not refer to any type of soil anchor.
- Type C: Manufactured homes with Type C foundations receive support from reinforced masonry or concrete piers only. The “C4” foundation has piers with a slab-on-grade (or “mat slab”). Vertical anchorage occurs at equally spaced points along the chassis beam lines only.
- Type E: With Type E, a perimeter structural wall is introduced in addition to interior piers along the chassis beam lines. This system is anchored for uplift and overturning at the exterior walls only.
- Type I: A foundation system supported at chassis and exterior walls but anchored for uplift and overturning at exterior piers only.
- Interior Piers: Piers nearest the marriage wall and supporting the chassis in multi-section units.
- Longitudinal Foundation Walls: Two walls beneath the long dimension of the unit (in its transport mode) which are structurally used as foundation shear walls that resist applied wind or seismic forces from the superstructure’s shear walls in the longitudinal direction.
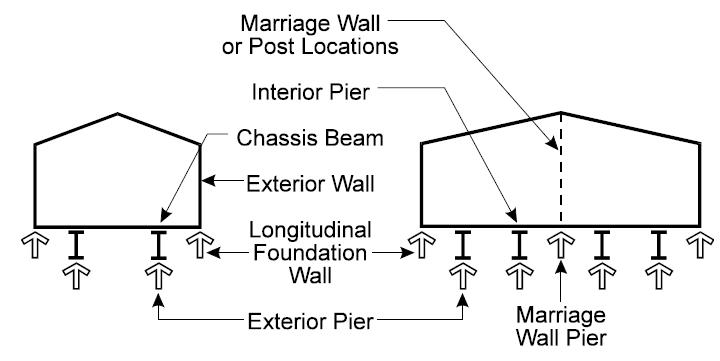
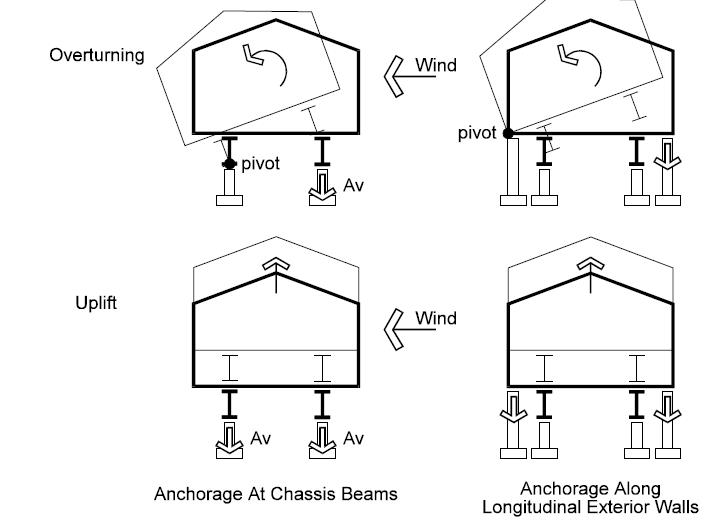
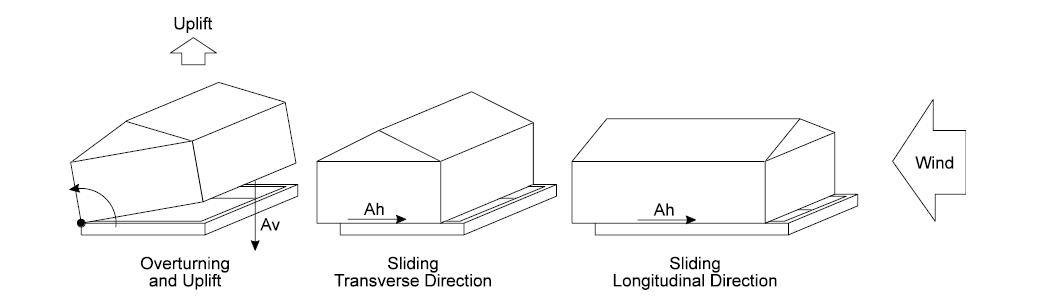
Pier and Ground Anchor Support System
The pier and ground anchor support system is perhaps the most common manufactured home foundation setup. This is due to the many advantages it affords, including its ability to easily adapt to local site conditions, its fast installation time, and the fact that it does not require dimensional precision during the foundation layout process.
The most frequently used configuration for pier and ground anchor support systems involves piers being installed under the main chassis beams and perimeter walls. These points are generally specified by the manufacturer. See figures 4 and 5 below for a typical example.
The downside to this system is that, in most cases, lenders and state and federal agencies do not consider it to be a “permanent foundation” – which means the property cannot be considered “real property.” There are exceptions, though. If anchors are fastened by other means other than the soil itself – e.g., encasing the anchors in a concrete slab-on-grade – then local jurisdictions may consider a foundation to be permanent.
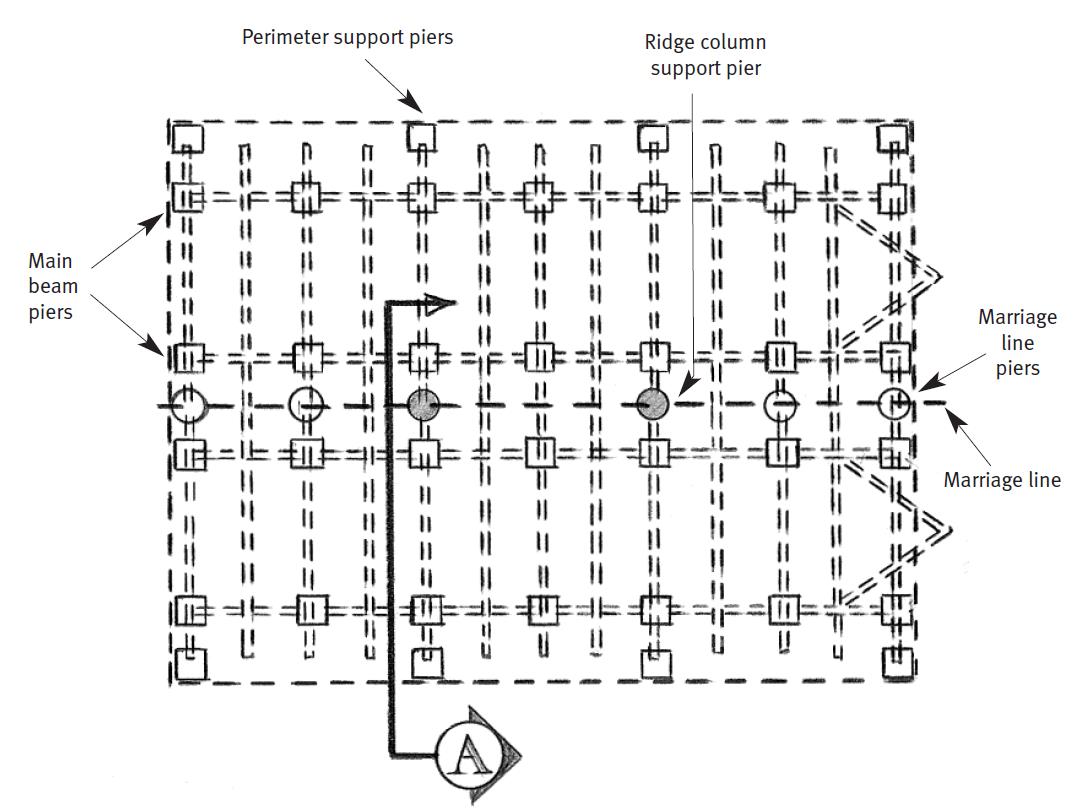
Photo courtesy of “Guide to Foundation and Support Systems for Manufactured Homes”
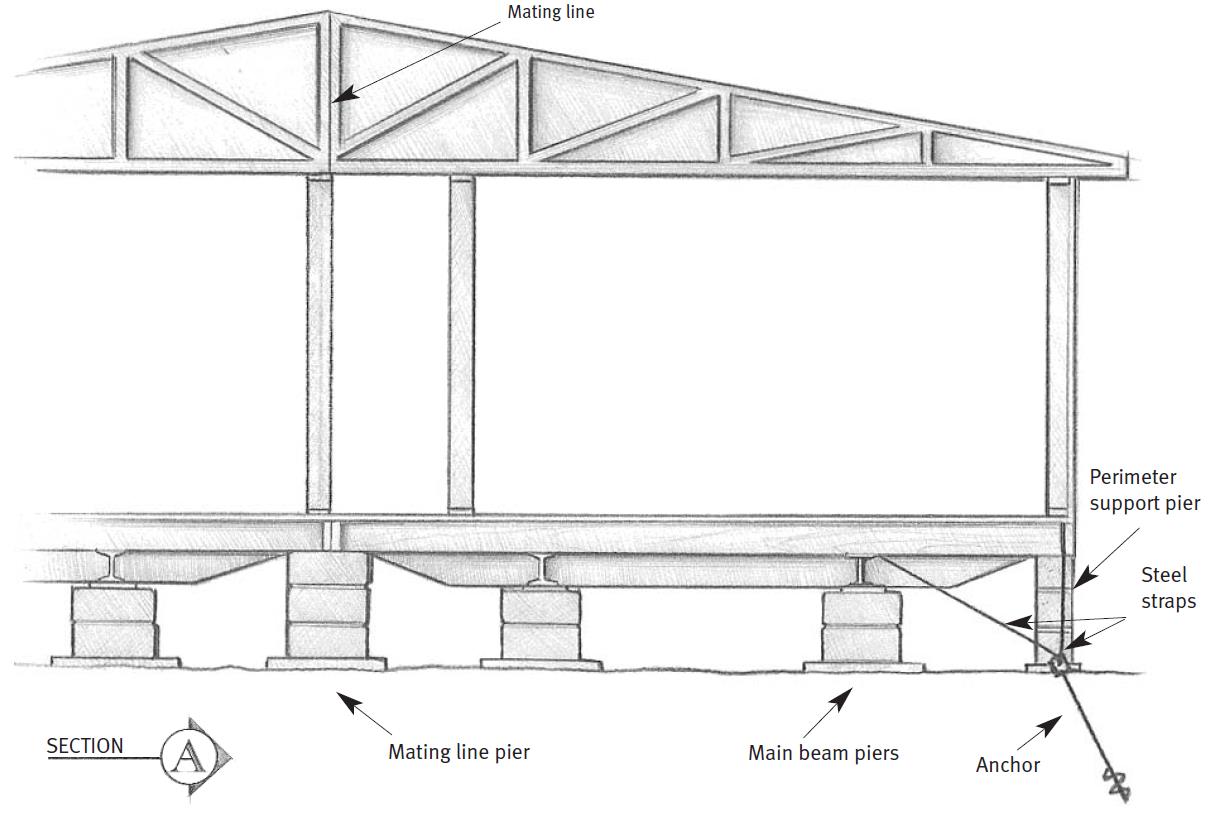
Photo courtesy of “Guide to Foundation and Support Systems for Manufactured Homes”
The spacing of the piers and the allowable bearing capacity of the soil determine the size (i.e., area) of the footer or pad. Bearing capacity is generally expressed in units of pounds per square foot (“psf”) and is classified in the range of 1500 to 4500 psf.
Well-graded gravels and gravel-sand mixtures containing little or no fine materials are considered excellent foundation materials (high-bearing capacity). Peat and other highly organic soils, on the other hand, are not suitable for foundations.
Hold-down devices are required to resist wind and uplift forces in this configuration. This is accomplished using auger-type (screw-in) ground anchors, which are sized based on home floor width, I-beam spacing, pier height, and the wind zone where the dwelling is located. Anchors are chosen taking into consideration their working load, length, and the width of the stabilizer plate.
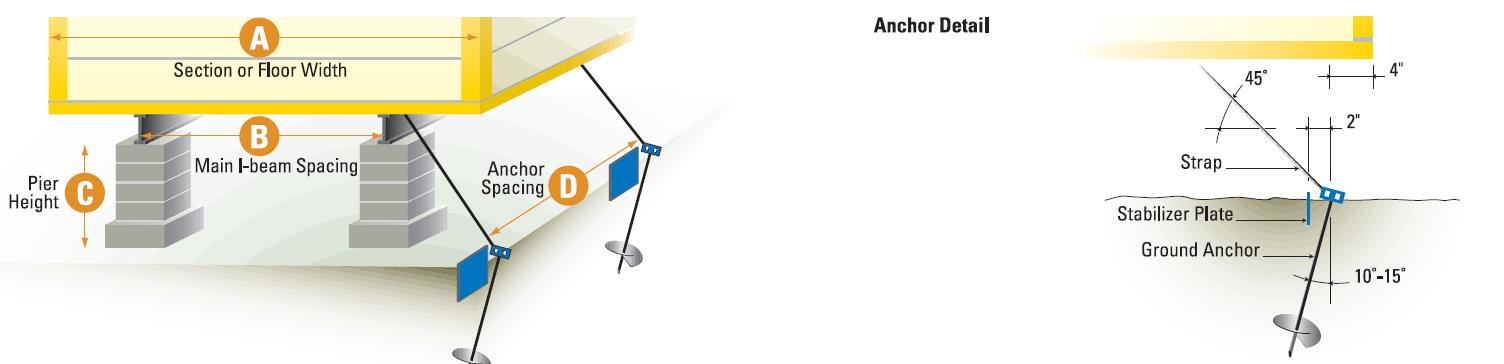
Crawl Space Systems
A crawl space system incorporates a full perimeter structural wall support (via either masonry or poured concrete) with an adequate space underneath for utility access and repairs.
Crawl spaces need not be considered habitable, but they do need to be accessible.
Crawl space foundation systems are intended for use where traditional site-builds are desired, as they qualify for real property financing.
This foundation is less suited to situations where economy, speed, or installation flexibility is paramount. With crawl spaces, much more care and effort are required to line up the foundation walls with the exact outside dimensions of the manufactured home.
Remember: manufactured homes are not site-built like traditional stick-framed dwellings, so a lot of coordination is required up-front with the vendor to ensure a foundation is true to fit.
Another factor that comes into play with crawl spaces is ventilation. As per your local AHJ, the under-floor space between the bottom of the floor joists and the earth under any building (except space occupied by a basement) should have ventilation openings through foundation walls or exterior walls. The minimum net area of ventilation openings must be not less than 1 square foot for every 150 square feet of under-floor space area, unless the ground surface is covered by a Class 1 vapor retarder material. Where a Class 1 vapor retarder material is used, the minimum net area of ventilation openings can be reduced to not less than 1 square foot for every 1,500 square feet of under-floor space area. One such ventilating opening must be within 3 feet of each corner of the building.
With the structural perimeter wall in place, a home can be securely attached to its foundation to resist wind, gravity, and seismic forces, as required. This is accomplished in the same fashion a traditional home is constructed. That is, the sill plate is attached via anchor bolts that have sufficient embedment length and on-center spacing as shown in the figures below:
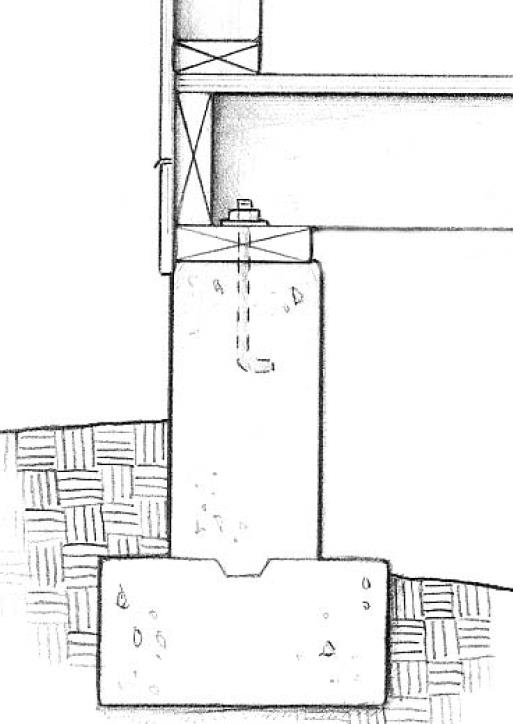
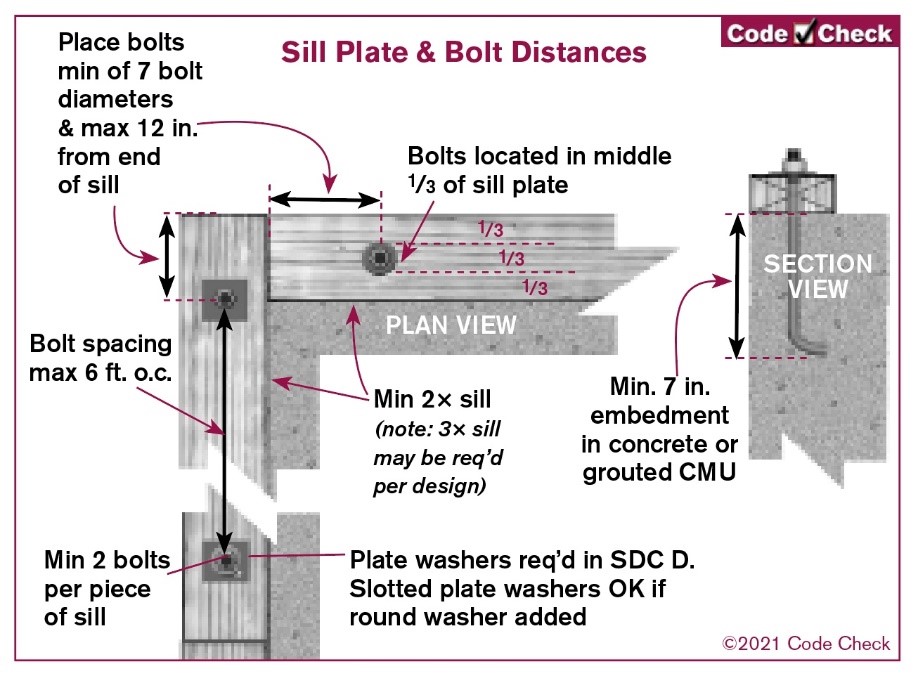
Note: This is considered a “Type E” foundation according to HUD code, due to the anchorage points.
The crawl space must also meet the following the minimum clearances:
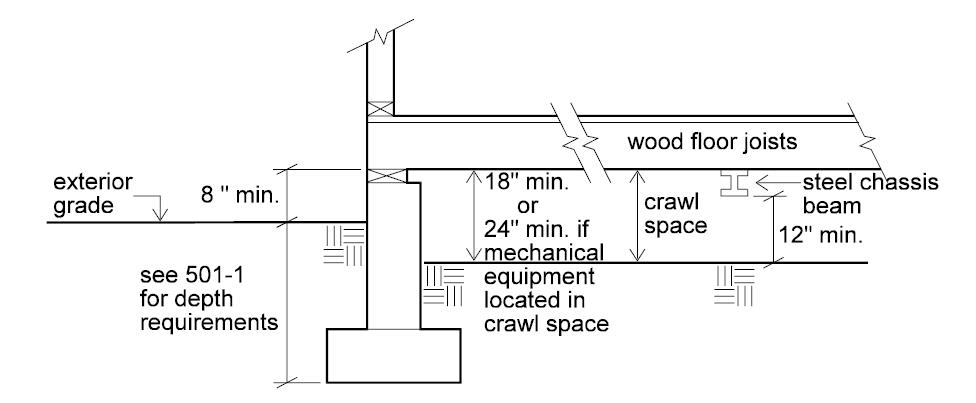
Slabs-on-Grade (“Mat Slab”)
With manufactured homes, slabs-on-grade differ from traditional stick-built homes, as slabs-on-grade only serve as a platform for a home. That is, they do not act as a home’s floor, allowing it to receive a finished surface such as linoleum, carpeting, tile, and so on.
A slab simply serves as a platform to provide structural support under the main chassis beams.
This is illustrated in the below figure:
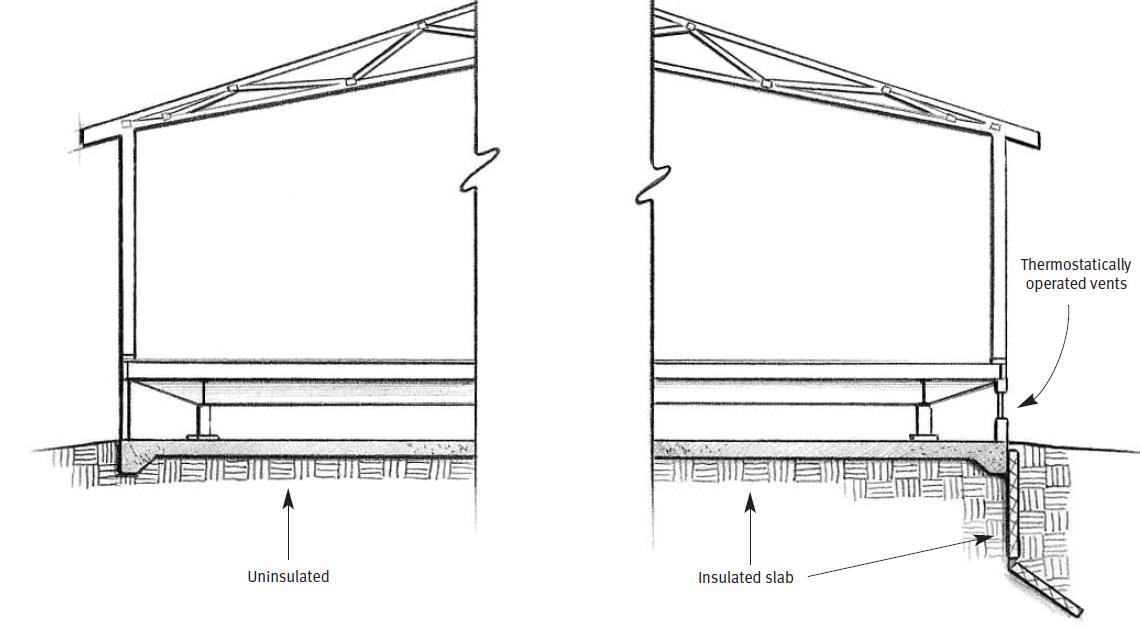
Photo courtesy of “Guide to Foundation and Support Systems for Manufactured Homes”
Slabs-on-grade foundations are beneficial in cases where adverse ground conditions, such freezing and expansive soils, are present. In such cases, slabs can effectively “float,” shifting as the soil underneath expands and contracts due to forces such as frost heave.
However, it’s important to keep the ground under your home dry using drain tile and sump pumps – this greatly minimizes or even eliminates soil movement.
Adding rigid insulation at the perimeter of a floating slab is referred to as a “shallow frost-protected foundation.” This design concept creates a thermal barrier. It keeps the slab warmer than the surrounding soil and will minimize the chance of the ground freezing underneath, preventing frost heave.
Although subject to review by the AHJ, an insulated slab may qualify as a real property foundation.
A home must be permanently anchored to its foundation to prevent uplift and sliding action in high-wind conditions. This can be done in a variety of ways, including embedding anchor straps in the concrete or using welded or bolted connections between the chassis and piers, if the piers themselves are permanent (e.g., mortared and grouted concrete blocks).
Basements
If your outdoor activities are curtailed during the winter months, then a full basement may be a solid option. Full basements provide an excellent structural support system and extend your home’s living space. Basements are an integral part of home designs, including for site-built homes. This is particularly true for the intermountain west and the northeast regions of the US.
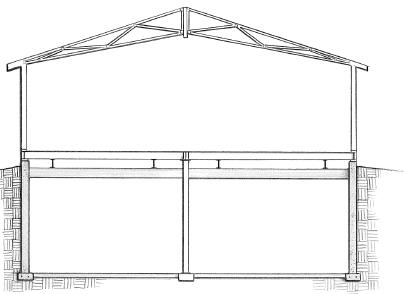
Photo courtesy of “Guide to Foundation and Support Systems for Manufactured Homes”
Depending on the grade of your site, basements can be built in many variations. These include a “walk-out” basement with a rear yard, a basement completely above ground, creating a split-level concept, or a “low profile” type installation.
Although basements come with a higher price tag, they’re considered a real property foundation, add usable space, and provide protection from deep frost and seismic action.
As is the case with crawl space construction, basements demand extreme care when laying out foundation walls. With site-built homes, carpenters can correct foundation errors by compensating with the floor framing. But unfortunately, this is not the case with manufactured homes. The outside wall cannot be longer or wider than the floor of the manufactured home.
Having your basement walls protrude horizontally beyond the edge of the floor joists can also cause headaches. So, always confirm your home’s exact floor dimensions with the manufacturer prior to laying out the foundation.
Coordination with anchorage and the securing of the home to its foundation also need to be carefully thought out. Since anchor bolts can conflict with floor joists, contractors prefer foundation straps – they offer more flexibility in the layout.
Always be sure to coordinate your foundation type with your home’s manufacturer to ensure compatibility.
Concluding Remarks
There are myriad factors to consider when deciding on a foundation support system for your manufactured home. Ultimately, your choice will boil down to your budget and personal preference.
There is no single “best” foundation system, but you do want to ensure that whatever system you choose is built in accordance with applicable codes. You should also be mindful of pitfalls associated with the design and construction process.
If you are looking for guidance or an inspection of an existing foundation, please don’t hesitate to contact the experienced, licensed engineers at W.D. Hill Engineering.
Structural Disclaimer:
This article is intended for information purposes only. It is not intended to relieve the user of this article of responsibility for a proper condition assessment and structural evaluation by an experienced licensed qualified design professional.