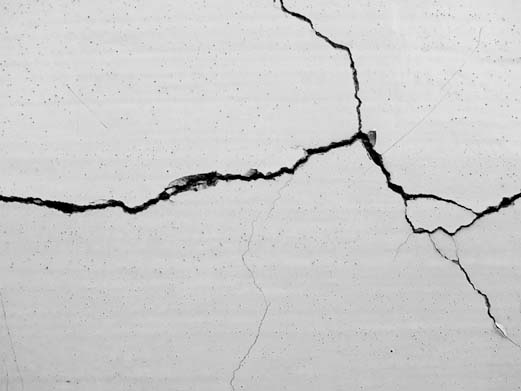
Concrete Cracks: Should I be concerned?
In life, certain things are inevitable. For concrete, cracking is one of those inevitabilities.
Concrete is a combination of three key ingredients: Portland cement, aggregate (usually sand and gravel), and water. When water is added to cement, a chemical reaction called “hydration” takes place – hydration works to bind everything together to form a durable, rocklike mass.
More water makes the concrete more workable, while additional cement paste increases concrete’s strength. The ratio of water to cement is referred to by engineers and contractors as the “mix design.”
In concrete, there are many variables that contribute to crack formation. Cracks may be attributed to either the original design mix, the installation process, or both. It’s often quite difficult to prevent all cracks from happening so hiring an experienced concrete contractor is always your best bet.
Despite the ubiquity of cracks in concrete, a scientific survey showed that cracks between 0.01” and 0.013” on easily observed, clean, smooth surfaces can lead to public concern (ACI Committee 224). Perhaps for this reason, clients often ask us, structural engineers, about concrete cracks in their homes. People want to know if cracks are a cause for concern.
While cracks’ severity can range from situation to situation, any significant isolated crack (over ¼” in width) should be referred to a structural engineer. These cracks may be “structural cracks,” i.e., cracks caused by excessive weight or deflection. Building elements with structural cracks are usually deemed unfit for their intended purpose.
If a crack seems to be widening, that may also be evidence that it is a structural crack. Loading on concrete causes cracks to widen and lengthen over time.
You may be relieved to find out, though, that most cracks are not structural in nature. Most cracks are simply caused by expansion and contraction, which is in turn caused by changes in moisture content and temperature. Expansion and contraction cracks typically do not represent a structural concern. Opting to repair them is your personal preference, and it boils down to what you can live with from a cosmetic standpoint.
Causes of Cracking
Cracks occur in concrete because concrete is roughly 10 times stronger when loaded in compression than when loaded in tension (i.e., when it tends to be pulled apart).
Because of this weakness, cracks develop whenever loads, restrained shrinkage, or temperature changes give rise to tensile stresses that are higher than the actual tensile strength of the concrete. Refer to figure 1 below (Figure courtesy of ACI 224R-16).
Engineers are aware of this problem. Where situations call for it, concrete’s strength is increased by manually adding reinforcing steel bars. This is known as “rebar.”
Rebar resists tension forces well beyond what concrete could do on its own. When concrete with rebar does crack, its cracks tend to be much smaller. Concrete that incorporates rebar is known as “reinforced concrete.”
“Plain concrete,” on the other hand, contains no reinforcement. Plain concrete walls are commonly used for basement wall construction, and for residential and light commercial buildings in low or non-seismic areas. Plain concrete offers little protection or ability to maintain its integrity when cracked.
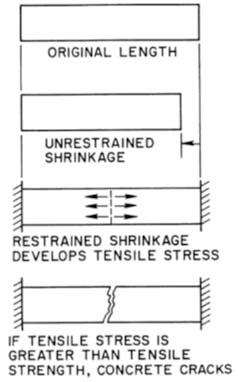
Plastic Shrinkage
This commonly occurs in concrete slabs. A slab is a concrete floor surface such as an exterior patio, garage, or basement. Even with the best floor designs and proper construction, it is unrealistic to expect completely crack- and curl-free floors (ACI 302.1-04).
Plastic shrinkage refers to volume change that occurs when the concrete is still fresh after placement, before it hardens (i.e., it is still in a semi-liquid state). When moisture evaporates from the surface of freshly placed concrete faster than it is replaced by water, the surface of concrete shrinks.
This is especially common when there is an underlying vapor barrier present. In such situations, water is allowed to only escape through the surface, and the top face of the slab will shrink more than the bottom. This can cause curling and set up tensile stresses that can cause cracking down the road.
Cracks associated with plastic shrinkage often resemble surface tears. They can be wide – as much as 1/8” – and their lengths can vary from a few inches to many feet.
Thankfully, steps can be taken during the finishing process to prevent rapid moisture loss during hot weather and dry winds. These measures include the use of fog nozzles, windbreaks, and sunshades, and covering the concrete’s surface in plastic sheeting.
Always discuss weather conditions and finishing requirements with your contractor to minimize the incidence of shrinkage cracks.
Drying Shrinkage
Hardened concrete expands slightly with an increase of moisture, and it contracts when moisture is lost. Moisture-induced volume changes are a key characteristic of concrete. Unfortunately, it is the combination of shrinkage and restraint that causes tensile stresses to develop in concrete.
Visual examinations of concrete structures will typically show random cracks a few inches in depth. Cracks tend to form at 90-degree angles.
Shortening restraint can be reduced by providing adequate contraction joints (sometimes referred to as control joints) in both slabs and walls at the time of construction. Providing joints in plain concrete is the only means of controlling and, thereby, relieving the buildup of such tensile stresses caused by shrinkage.
According to the Portland Cement Association, contraction joints for slabs on a grade should be spaced at distances (in feet) of 24 to 36 times the slab thickness (in inches) to control random cracks. So, if the slab is 4” thick, joints should be placed every 8 to 12 feet. Joints in walls are equally important for crack control – generally, these are placed every 20 feet.
Differential Foundation Settlement
The lowest part of a structure is referred to as its “foundation.” The primary function of a foundation is to transfer the load of the structure to the underlying soil without overstressing it. Overstressing soil can lead to either excessive settlement or shear failure of the soil, both of which can cause damage and cracking to a foundation – not a good problem to have.
All structures settle in some fashion. With respect to foundations, settlement occurs whenever the structural weight on the footing exceeds the bearing strength of the underlying soil. The degree of that settlement will depend on soil type, the amount of ground or surface water, the slope of the lot, and so on.
Cracks in foundation walls are a common symptom of foundation settlement.
In residential construction, contractors will often backfill using the same material that they dug out to place the foundation. If that “native” backfill contains mixed organics, such as vegetation or even large tree or root systems, these will decay over time and cause large voids to occur. In addition, backfill is often not properly imported or compacted – while this saves on costs, it can cause settlement problems down the line.
Another common settling problem occurs when a foundation is placed on clay-rich soil. Geotechnical engineers characterize clay soils as “highly plastic.” They behave “actively” over a wide range of moisture contents.
Plastic soils physically shrink in volume when they dry and swell in volume when they become wet. As clay soil shrinks and swells underneath your foundation, it can cause problems.
With all soils, proper site drainage is imperative. That’s because the soils underneath foundations must maintain a uniform moisture content. If water stands or collects in low-lying areas near foundation walls, the subgrade soils can become and/or remain saturated even as adjacent soil remains dry.
So, now that we’ve gotten a good idea of what causes settlement in foundations, we’ll move on to defining differential settlement.
When settlement is not uniform – e.g., one side of a building settles more than the other – it is referred to as “differential settlement.” Differential settlement causes an uneven stress distribution throughout a structure. In a house, it may cause annoyances such as sticking doors, windows, and sloping floors. It can also cause foundation walls and brick veneer to crack. Fortunately for you, differential foundation settlement eventually stabilizes, and conditions rarely deteriorate after the original settlement period.
But now here’s the rub. It’s impossible to determine whether the settlement is still active or not via a single inspection. That’s why structural engineers, such as the pros at W.D. Hill, recommend monitoring the size and number of cracks over time.
If other surfaces in your house have cracked – such as brick veneer and drywall, for example – discuss those issues with a structural engineer for proper recourse.
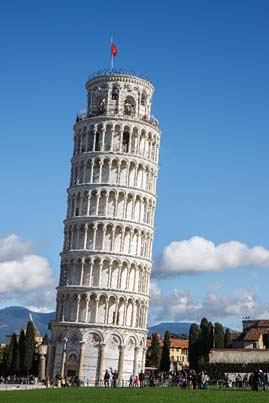
The Leaning Tower of Pisa – A classic example of differential settlement. The foundation was built on dense clay and near high ground-water.
Hydrostatic Pressure
Hydrostatic pressure is defined as the pressure exerted by standing water against a surface. If you live in a high ground-water area, at the toe of a hillside, or have improper water management on your property, hydrostatic pressure could cause you some headaches. When a constant force of water is applied to your basement walls, it can cause water intrusion and structural cracking over time.
The concept of hydrostatic pressure can be better understood by considering a diving submarine – the deeper the sub dives, the greater the pressure is exerted on its hull. Eventually, if it dives too deep, the hull of the submarine will be crushed. That’s because the weight of water is significant. In fact, the weight of water in just a 1ft. x 1ft. x 1ft. cube weighs about 62 pounds – and this pressure increases linearly with depth.
Let’s consider how significant a force of water can exert on your basement.
Say you have a basement wall that is 9 ft. high by 20 ft. wide and say the soil next to your foundation is completely saturated with water. That water pressure would apply a resultant force of about 50,000 pounds on your wall! And that is in addition to the lateral earth pressure already present thanks to the backfill.
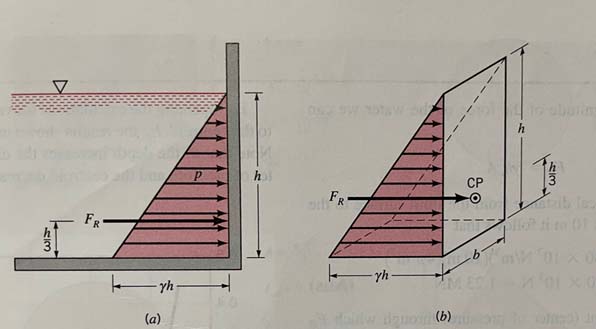
Photo Courtesy of: A Brief Introduction to Fluid Mechanics, 4th Edition
It’s no wonder that hydrostatic pressure can cause such serious damage.
Leaking and flooding are the most obvious signs of hydrostatic pressure, and if a pressure issue is not addressed, it can cause consequential structural damage to the foundation.
If you have a wall that is bowing inward and has a horizontal crack (usually located about one-third or midway from the bottom of the wall), you should call a structural engineer as soon as possible. Bowing and cracking of this type is indicative of damage caused by hydrostatic pressure. This is most associated with land grade issues, such as uphill walls on sloping lots or improperly graded sites.
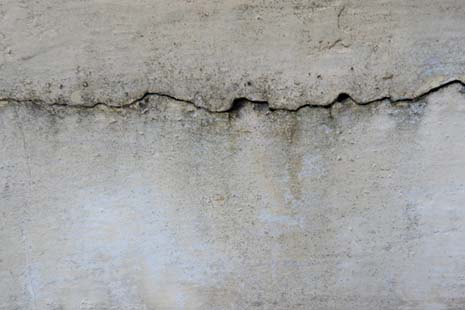
Evaluation of Cracking
Since engineering and construction data regarding the construction of your home is likely not available, engineers such as us rely on condition surveys and visual inspections of properties. Through info gathering activities like these, we examine exposed concrete, the surrounding grounds, and pull any readily available geological information. These steps help us establish the cause of cracking. Cracking is usually due to one or more of the above-discussed causes:
- Hydrostatic pressure
- Geology/Soil properties
- Foundation movement
- Mix design and poor construction practices
When surveying, we describe cracks using surface appearance, depth, location/frequency, and width. General terms and descriptions are outlined below:
- Surface appearance
- Pattern: These are short, interconnected, and run in all directions (sometimes referred to as “map” or “craze” cracking) – See Figure 4
- Isolated: Individual vertical, horizontal, diagonal, longitudinal, or transverse
- Width
- Fine: Less than 1/8 of an inch (Negligible/no cause for concern)
- Medium: 3/16 to 9/16 of an inch (Moderate/slight concern)
- Large: 9/16 to 1 inch (Severe/cause for concern)
- Very Large: Over 1 inch (Very severe/serious concern)
- Depth includes surface, shallow, deep, and through
Also its important to consider is the state of a crack’s activity: is it active or dormant? (See Figures 3 and 4). An active crack is still working – i.e., the mechanism that is causing the cracking still exists. Dormant cracks are nonworking, meaning the cause of cracking has been removed or greatly minimized.
Selection and Methods of Crack Repair
A common misconception is that once you fix a crack, the problem is solved. However, it is important to differentiate a defect from the actual cause of the defect, and it is equally important that the cause of a defect is corrected before meaningful repairs are made.
Figures 3 and 4 are decision trees. These can aid in the selection of an appropriate repair method. The first step is to determine whether the crack is active or dormant. This can be done by monitoring the crack and periodically measuring its overall width and length. If it is still active, then it’s recommended that you (or an engineer) remove or reduce the mechanism creating the issue prior to performing a repair.
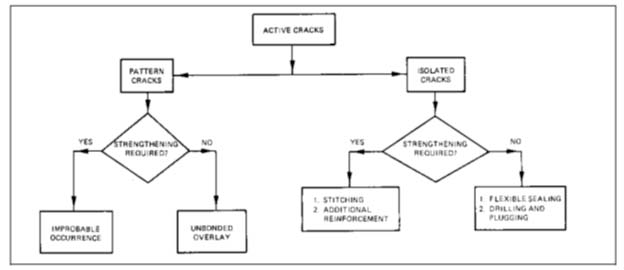
Courtesy of Johnson, S.M. 1965, Deterioration, Maintenance, and Repair of Structures, McGraw-Hill, New York
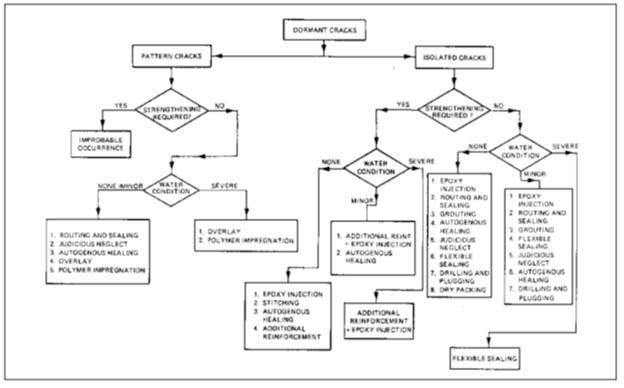
Courtesy of Johnson, S.M. 1965, Deterioration, Maintenance, and Repair of Structures, McGraw-Hill, New York
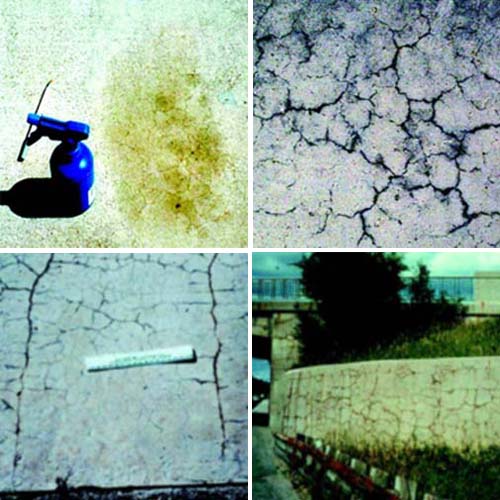
Photos Courtesy of ACI’s Guide for Conducting a Visual Inspection of Concrete (ACI 201.1R-08)
When to Call in a Structural Engineer
If you have a crack that’s over 1/8” in width and/or seems to be expanding, it’s probably time to call in a structural engineer. Additionally, if you’ve got a basement wall that’s bowing and cracking near its midsection (regardless of the depth of the crack), it’s also a good idea to call a structural engineer.
In both these situations, failing to address the problems behind the cracking can lead to further, much costlier damage down the road.
At W.D. Hill, we’ve got the experience and expertise necessary to both monitor cracks, diagnose their underlying causes, and propose long-term solutions.
Structural Disclaimer:
This article is intended for information purposes only. It is not intended to relieve the user of this article of responsibility for a proper condition assessment and structural evaluation by an experienced licensed qualified design professional.